NFPA 1851 Guidance
The National Fire Protection Association (NFPA) has developed PPE care and guidelines to protect the health and safety of the fire service. The NFPA 1851 standard was created to establish proper PPE maintenance and limit the exposure of fire ground contaminants to firefighters.
The NFPA 1851 Standard covers the selection, care, and maintenance of structural and proximity firefighting PPE. It is a comprehensive guide to keeping gear in top shape and maintaining peak performance while helping to reduce your risk of health and safety issues commonly associated with improper PPE maintenance, contamination, or wear.
At Gear Wash, we think it's important for all firefighters to follow NFPA 1851 guidelines; that is why we offer educational videos to any department interested in keeping current on standard updates and training on proper firefighting PPE cleaning, and inspection techniques.
NFPA 1851 Topics
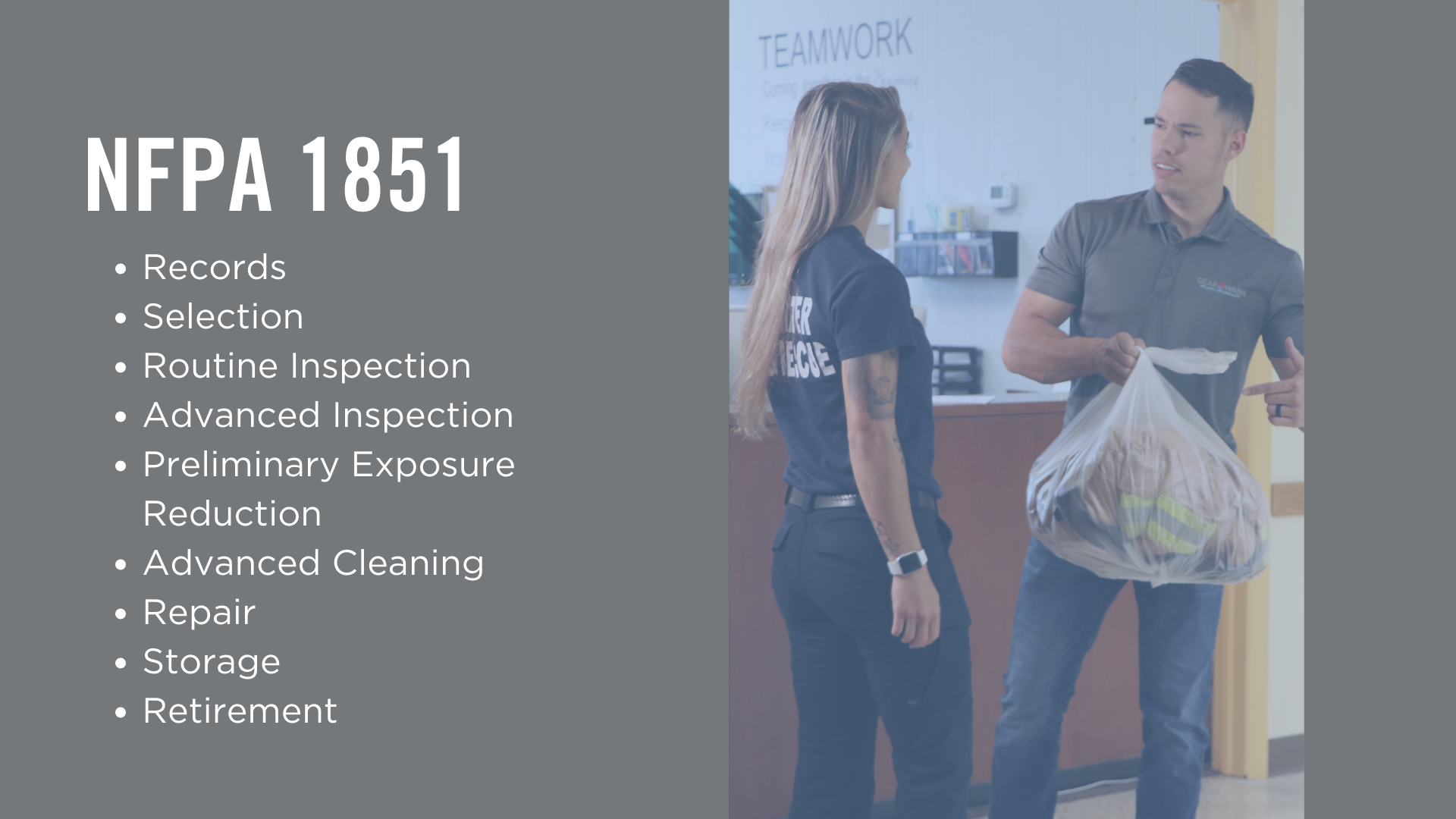
The guide provides chapters on the following topics. Skip directly to topic by selecting the section below.
Record Keeping
The standard requires documentation and maintenance of records on firefighting PPE elements, including rental and loaner gear. Record information should include:
- Whom gear is issued to
- Manufacturer details
- Inspections, cleanings, and repairs to the gear
- When gear is retired and its disposal method
Record keeping is aimed at reducing safety risks related to poorly maintained, contaminated, or damaged PPE. Explore our free record keeping system.
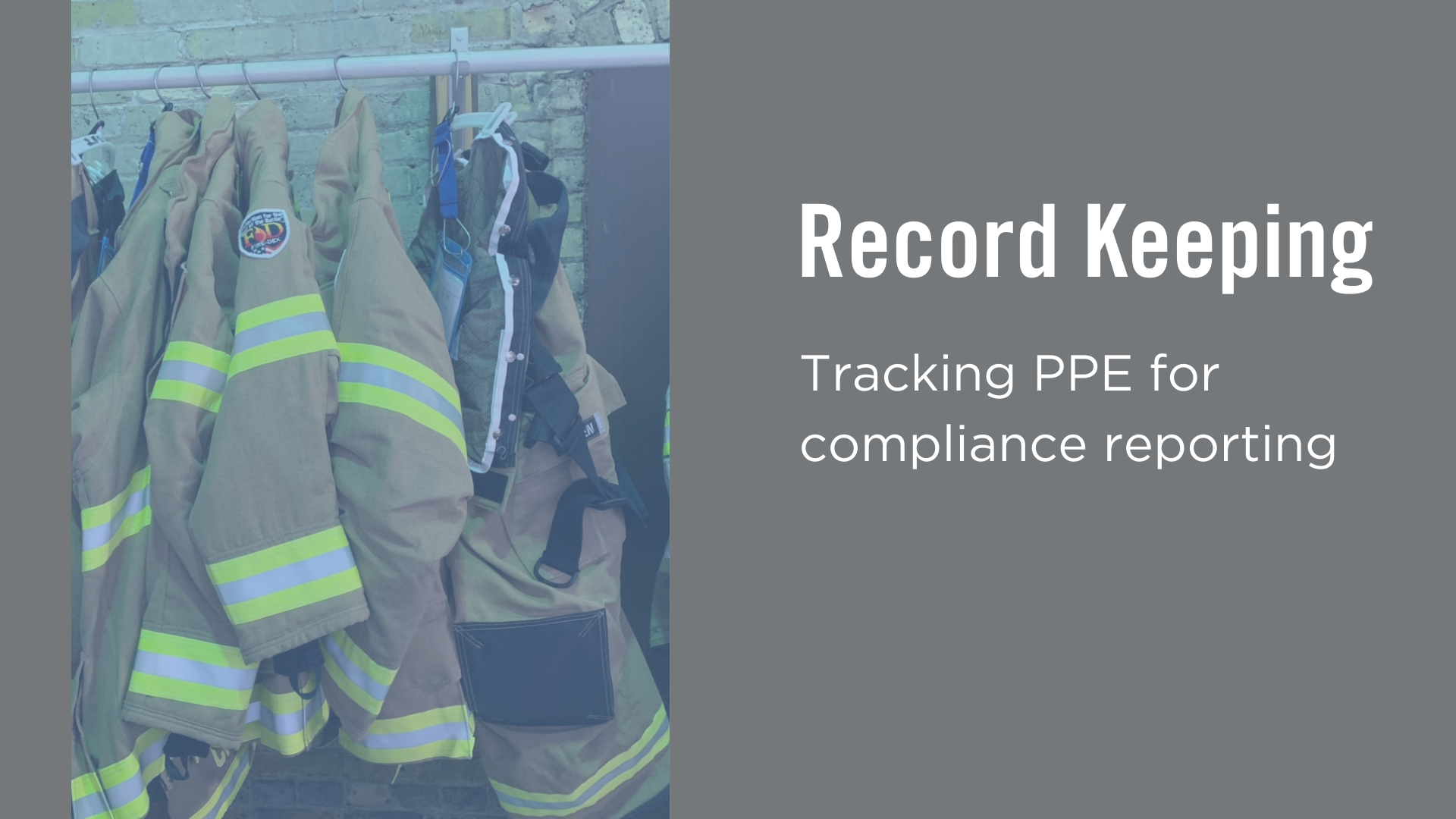
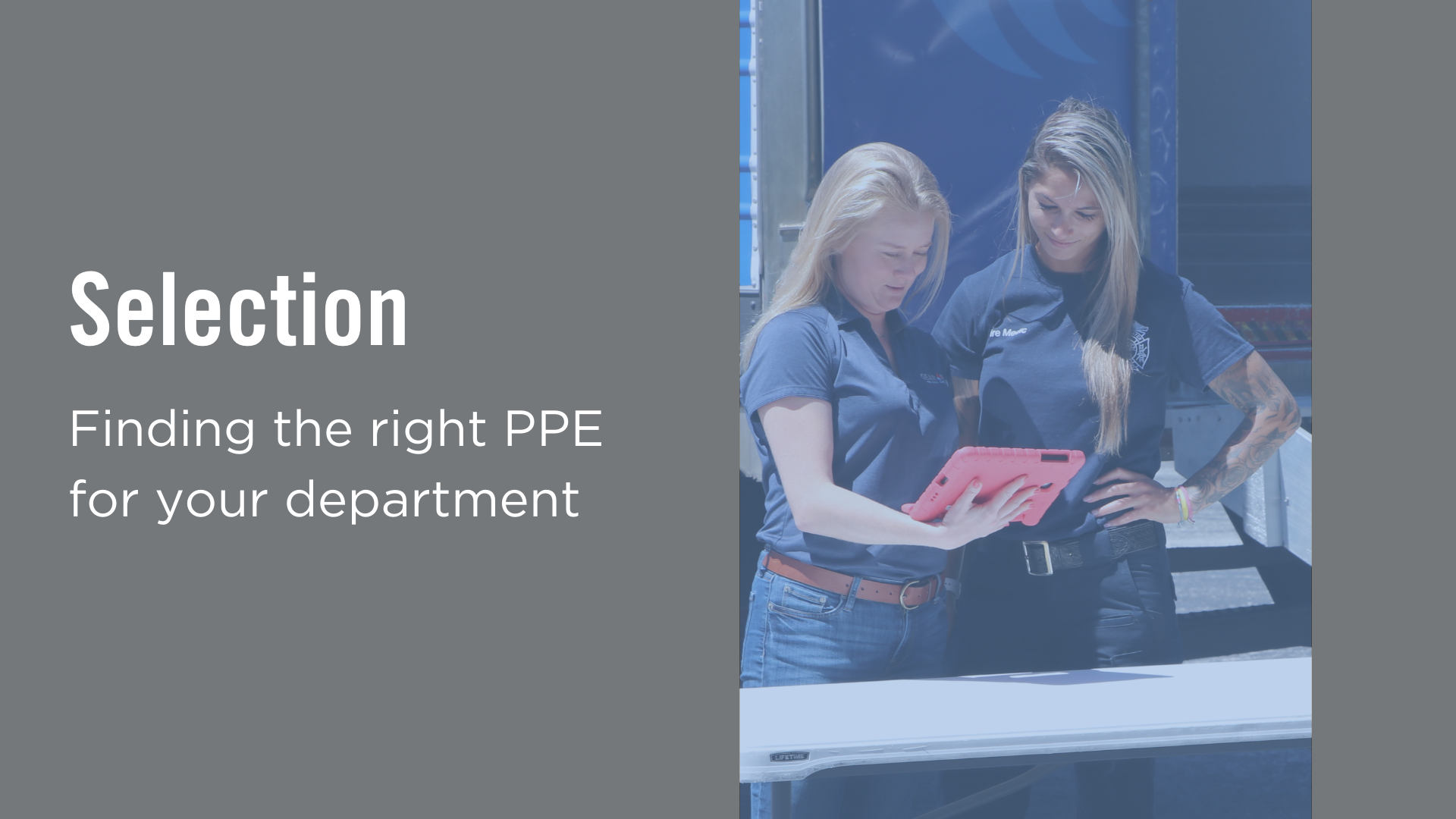
Selection
Prior to starting the selection process, a risk assessment should be performed in order to evaluate the comparative strengths and weaknesses of the elements under consideration, ensure the proper interface between ensemble elements, and confirm the PPE is suitable for the hazards your fire department will encounter.
A field evaluation may be conducted in order to compare the performance of the products.
Routine Inspection
Before and after wearing your gear, check for wear and tear! If you see something say something, as soon as possible. You want to keep up on minor repairs before they become irreparable. Individual members of your department should conduct a Routine Inspection of their PPE at the beginning of each shift and after each use to inspect for soiling, contamination, or physical damage. If the gear fails any part of this inspection, an Advanced Inspection should be performed.
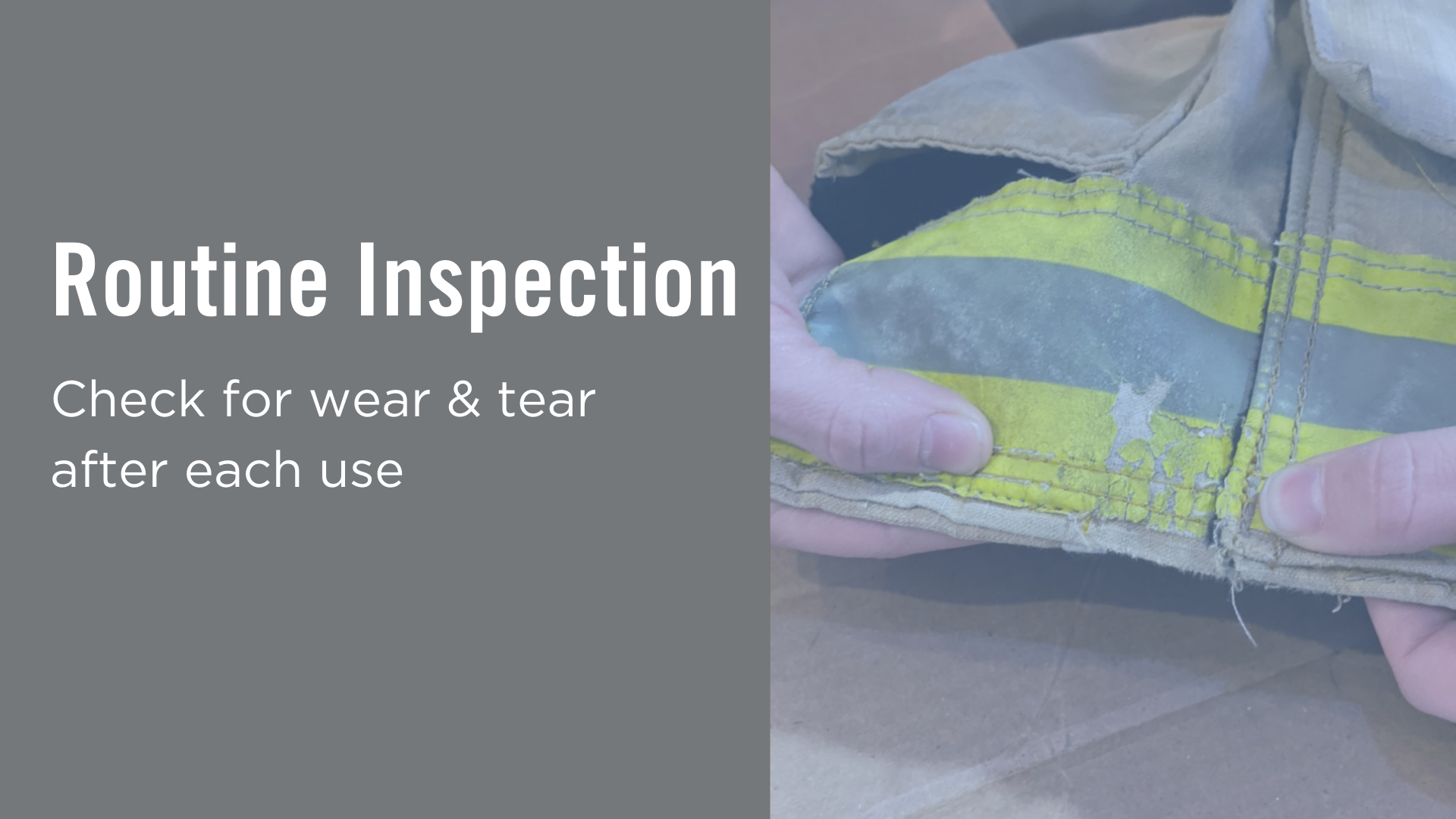
What is an ISP?
An Independent Service Provider (ISP), is an organization that performs advanced cleaning, advanced inspection, and advanced repairs of firefighting PPE. An ISP must be audited by a third party and go through annual third party verification to provide these services. This ensures that the organization demonstrates excellent cleaning, inspecting, and repairing of garments as maintained by the NFPA 1851 standard.
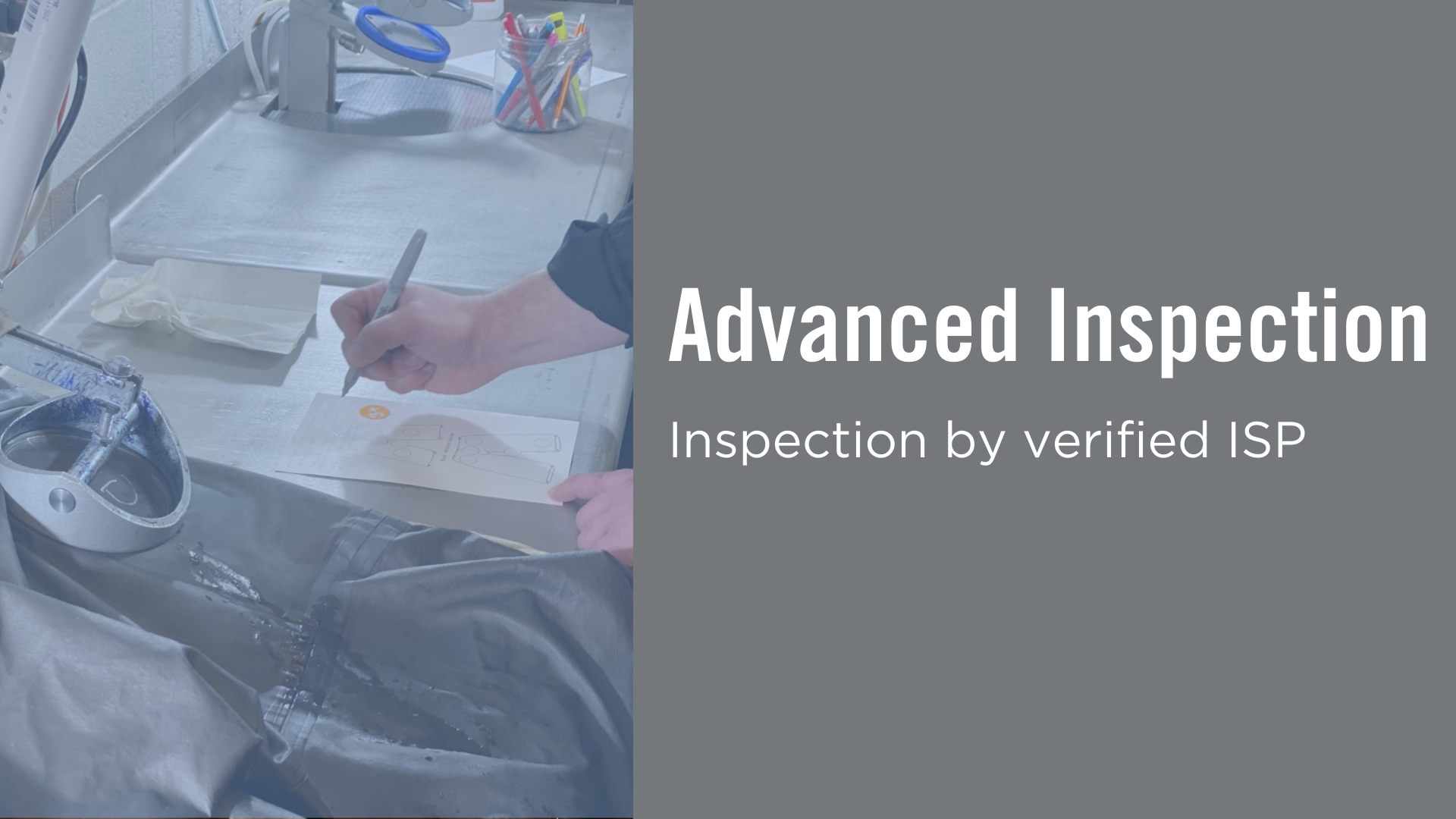
Preliminary Exposure Reduction
End users should perform Preliminary Exposure Reduction immediately after exiting the emergency scene at any incident where their gear has become soiled or contaminated. Dry or wet mitigation techniques must be conducted prior to the removal of PPE and then elements must be isolated and bagged. Where possible, bagged elements shall not be transported in the passenger areas of the apparatus or personal vehicles.
Following Preliminary Exposure Reduction, an Advanced Cleaning should be performed.
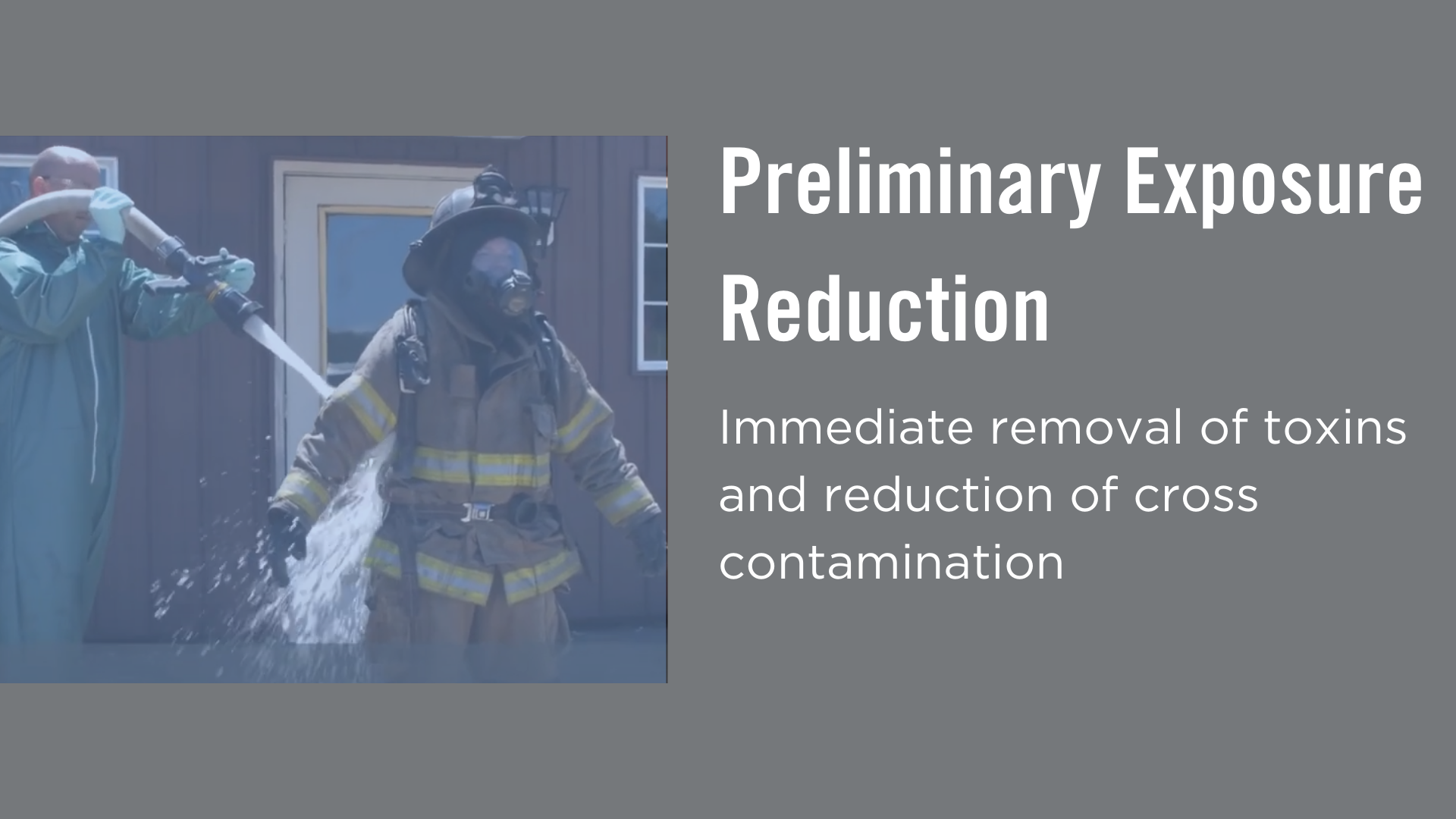
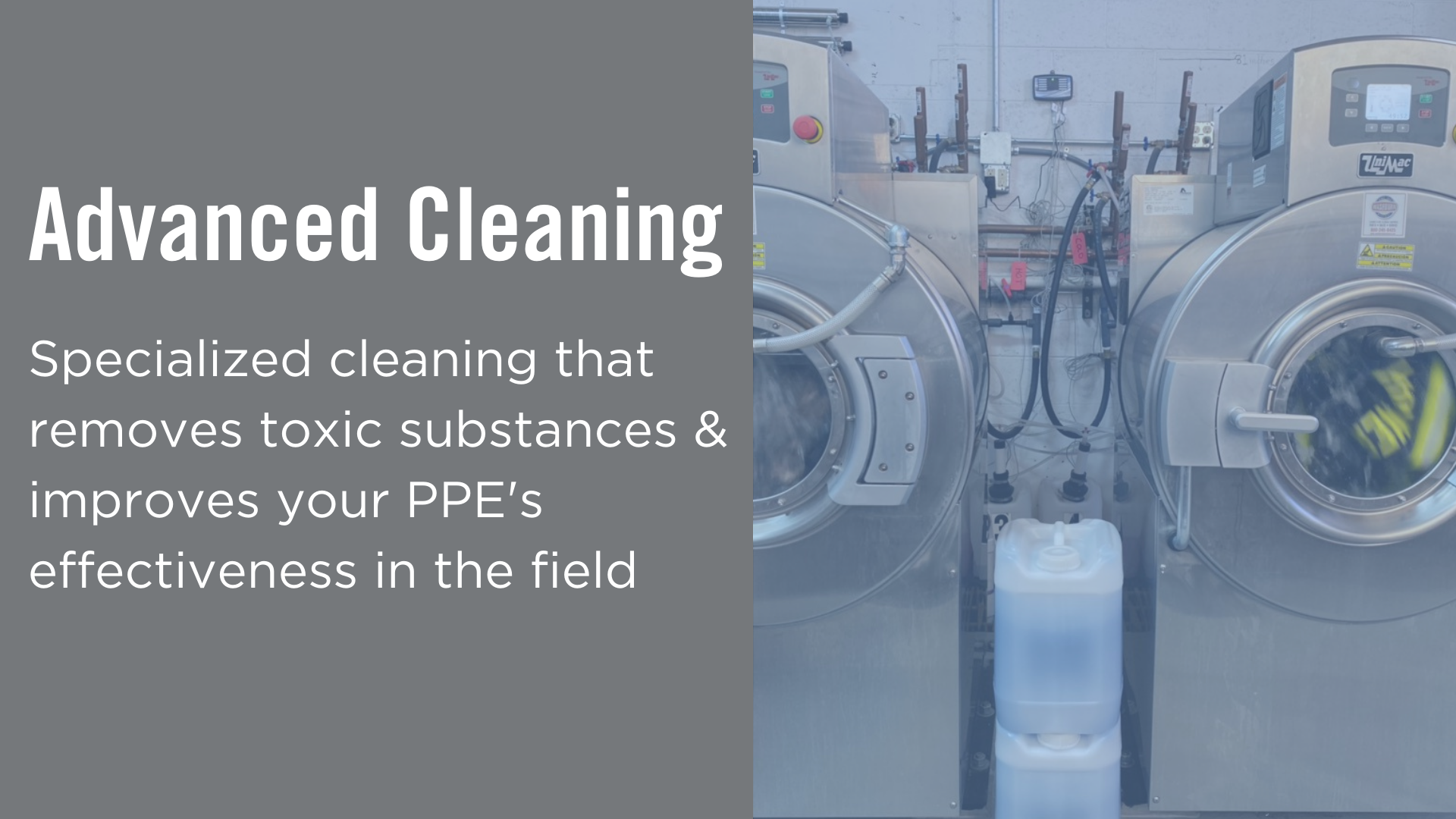
Advanced Cleaning
Departments are required to complete two Advanced Cleanings per year, and whenever protective clothing is exposed to combustible materials (AKA what we refer to as “the yuck” from smoke particulates). The “salty” image is no longer recognized as a badge of honor, it’s a serious health risk. Accumulated soot or substances on turnout gear can have negative effects on your gear’s ability to keep you protected. These requirements verify the effectiveness of cleaning procedures used to remove toxic substances from PPE. It’s important that helmets, boots, gloves, and hoods are inspected and cleaned to ensure maximum use.
Advanced Cleanings must be performed by the element manufacturer, a manufacturer trained organization, a verified organization, or a verified ISP. Gear that is soiled, shall receive advanced cleaning prior to reuse.
Learn how we care for your gear during an advanced cleaning.
Storage
Prolonged exposure to UV rays and fluorescent lighting can damage your turnout gear. Keeping your gear tucked away from harsh lighting will help protect it. Before storing firefighting PPE, your garments should be clean and dry, avoiding contact with contaminants, such as oils, solvents, acids or alkalis.
The storage areas must be well ventilated, with no exposure to harshful lighting; fluorescent lighting, direct sunlight, and indirect sunlight. PPE should not be stored at temperatures below -32C (-25F) or above 82C (180F).
When transporting, PPE should be placed in an airtight protective case or bag to prevent damage.
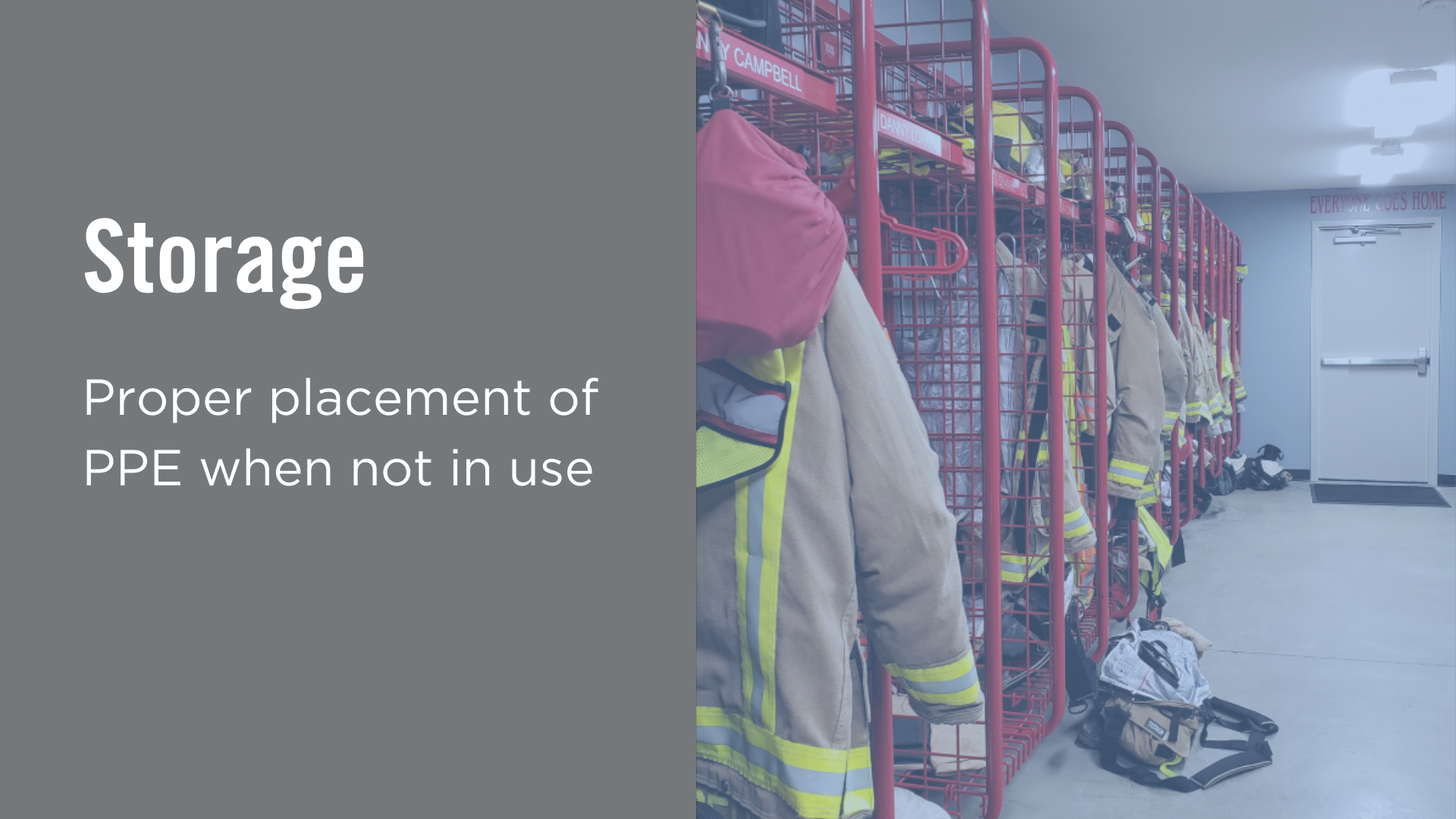
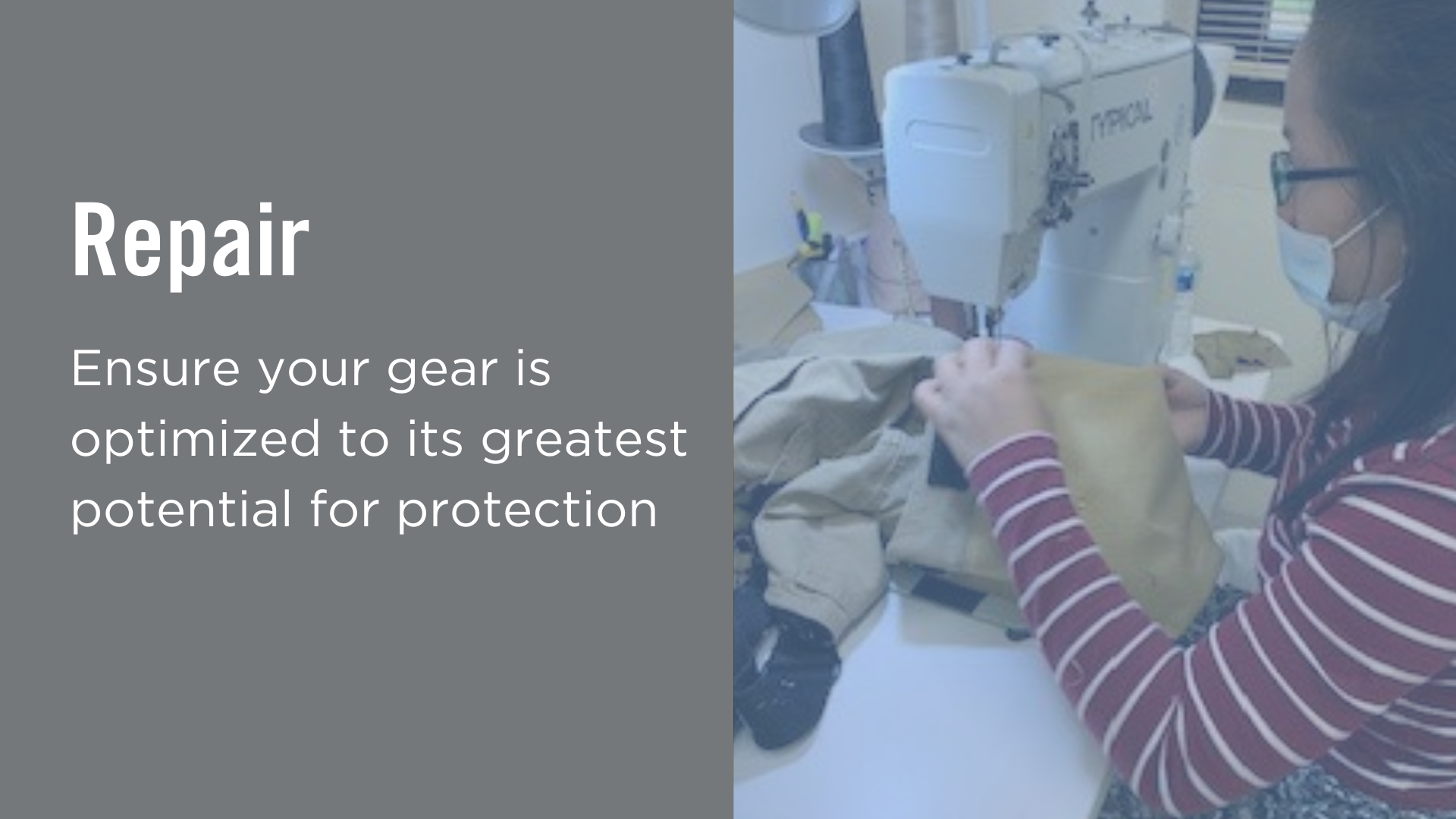
Repair
It’s important to send your gear to an ISP when repairs are needed. It’s much more cost effective to repair turnout gear than to replace it. All repairs must be performed by:
- The original manufacturer
- A verified and trained ISP or
- A member of the organization who has received training
Keep in mind, an Advanced Cleaning should be performed prior to repair. All repairs and alterations must use materials and components that are compliant with NFPA 1971.
Retirement
Eventually, your firefighting PPE will need to be replaced. Structural turnout gear and ensemble elements should be retired no more than 10 years from the manufacturing date. Once the protective properties of the turnout gear have diminished, it is no longer safe to use. It's important to replace your turnout gear if:
- Contaminated
- Cleaning no longer restores it after being soiled
- Defective
- Worn or damaged beyond reasonable repair
- It’s not compliant with NFPA standards
- The workplace requirements have changed and the gear is no longer usable
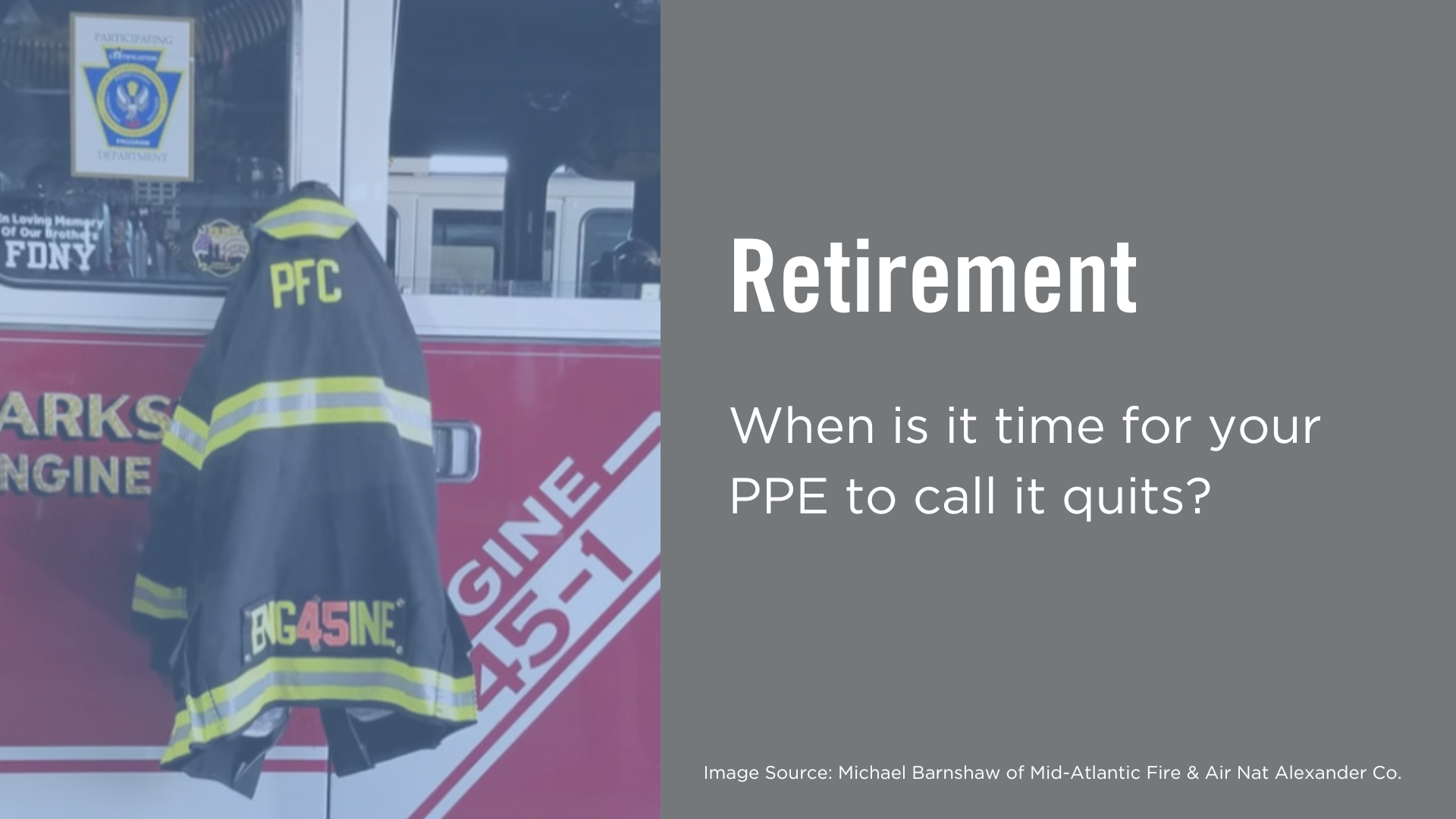